New coil technology for solenoid valves can increase energy efficiency by up to 80%. Bürkert’s Kick and Drop valve coils save significant cost by reducing energy use and extending service life. The increased efficiency also optimises environmental sustainability. With a low maximum operating temperature, the coils enhance safety and remove the potential of electrical overheating. The 3-in-1 design, covering various voltage inputs, also streamlines inventory management.
The new Kick and Drop coils can be used across a range of Bürkert solenoid valves, including pneumatic, plunger, servo-diaphragm, and servo-piston, as replacement demand or retrofit. Covering a variety of inrush and holding powers, each 3-in-1 coil covers DC, AC 50Hz and AC 60Hz, spanning 24V to 240V inputs, this flexibility reduces storage and handling requirements. Solenoid Valve Cummins
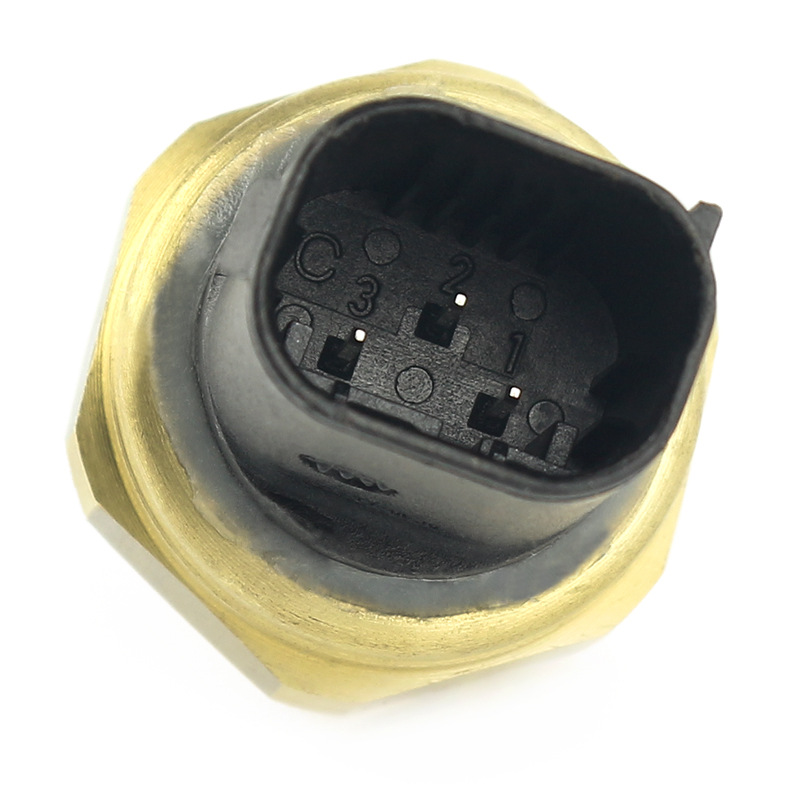
The device optimises energy efficiency by utilising a high initial voltage to move the valve into position. After just 500ms, the desired position is reached, and the coil wattage is reduced to a lower level that holds the valve position. This makes the coils well-suited to applications with long duty cycles. The increased ‘kick’ force is also useful for applications where the valve is required to open against a high-pressure differential.
The design includes two coil windings encapsulated in a single epoxy coil, with both coils powered in series. The first winding delivers the ‘kick’ that moves the plunger, while the second winding ensures the ‘drop’, and holds the plunger in position. The overexcited inrush winding generates a very high starting power, creating a strong magnetic field using 85% power to quickly move the plunger, but just 15% to hold it in position. In contrast, a standard valve coil produces a continuous magnetic field to move the valve into position and hold it over time. As a result, Kick and Drop coils can minimise the overall energy demand by up to 80%.
Reducing solenoid valve energy use can also make a significant contribution to improved sustainability. Taking an installation of 8,000 solenoid valves, Kick and Drop technology can save 114MWh per year and a CO2 reduction of 830 tons, based on 485 g/KWh.
Decreasing the continuous current requirement also extends the coil’s lifespan, reducing the total cost of ownership. For water applications, the Kick and Drop coils can also help to prevent the challenge of calcification, caused by hard water with high lime breakdown. Higher temperatures speed up the lime breakdown process, but below 60°C, the process is so slow that it doesn’t create a problem. The Kick and Drop coils only heat up to a maximum of 55°C, which removes the challenge.
As the coils only heat up to this lower maximum temperature, this increases safety by reducing the risk of burns. Kick and Drop coils can be used in insulated systems or housings, and the low operating temperature also prevents electrical overheating, with testing according to EN 60730-2-8.
The coils provide these advantages within a compact footprint, comparable to a standard coil, and they can also be used in close proximity to other electrical equipment as a result of noiseless EMC (electromagnetic) compliance.
http://www.burkert.co.uk
https://www.linkedin.com/company/burkertfluidcontrolsystemsuk&ireland/
Kick and Drop coils can minimise the overall energy demand by up to 80%.
SICK says its innovative new FTMg thermal flow meter simultaneously measures gas flow, pressure and temperature then computes the combined values to detect leaks in pneumatic systems and monitor compressed air energy consumption in real time.
In these days of pushing the boundaries on energy efficiency it’s very easy to connect a lower working temperature in a boiler to a lower flue gas temperature and therefore higher efficiency but is that really the case? The Combustion Engineering Association (CEA) explains further.
Andy Pye reports on June’s Talking Industry, which covered the topical subject of Energy Efficiency in Manufacturing.
To view a digital copy of the latest issue of Plant & Works Engineering, click here . View the past issue archive here . To subscribe to the journal please click here .
"How is your manufacturing business preparing for a net Zero target?"

Drain Solenoid Valve Click here to let us know about an event!