Turning Facility Data Into Bottomline Benefits » The First 100 Days as a Facility Manager » 2023 Vision Award Winners » Staffing Strategies from Recruitment to Retention »
If facility managers have seen the movie “The Shawshank Redemption,” they may recall the scene of the prisoners “hot mopping” the prison roof. That type of roof system was an asphalt “built-up roof” (BUR) system which has served buildings throughout North America for decades. Asphalt is the water-resistant material of choice since ancient times. Elastomeric Waterproofing Membrane
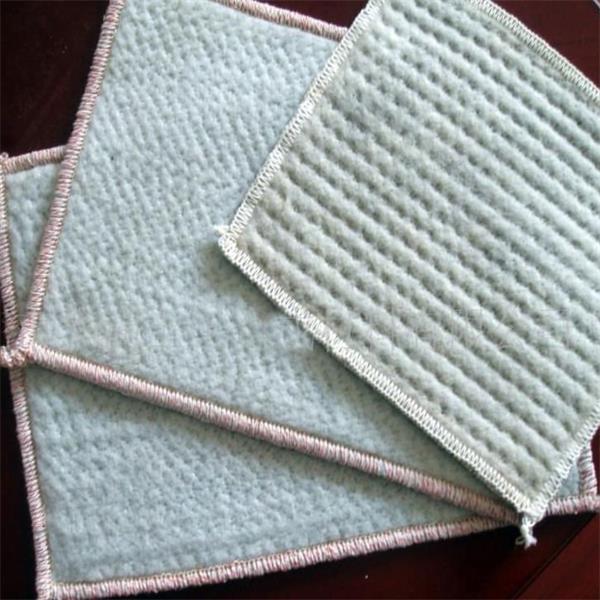
It’s doubtful readers own or oversee a 1940s-era prison, however, anyone can also benefit from the time-tested and time-proven reliability of a low-slope asphalt roof system. In fact, the odds are that an asphalt roofing system might be protecting the building right now. Manufactured and tested to strict standards and system performance requirements, their durability and resilience are impressive when correctly installed by trained and often certified professional contractors.
There are two types of asphalt-based low-slope roof systems. The first is the traditional BUR system mentioned above. BUR systems consist of adhesive layers of hot asphalt (bitumen) alternated with typically three or four layers of ply sheets, or felts, applied over the substrate system.
Although BUR systems are still going strong, a newer generation of multiple-layer asphalt roofing is now the more popular choice — the modified bitumen system (mod bit or MB). Developed in Europe in the ’60s and ’70s, modified bitumen roof systems are manufactured by combining a polymer, either atactic polypropylene (APP) or styrene butadiene styrene (SBS), with asphalt. The ‘modified bitumen’ coating or matrix is then reinforced with a scrim of polyester or fiberglass or a combination of the two. This matrix, whether APP or SBS, improves the bitumen’s resistance to ultraviolet light, its performance and flexibility at both high and low temperatures, and its ability to resist water penetration.
Individual MB sheets are then typically installed in two or sometimes three layers. The bottom (base) sheets and top layer (cap) sheets are adhered together in a variety of ways. Most commonly, they are mopped down using hot asphalt or heat-welded to melt the coating. Alternative installation methods allow for cold-process adhesives with low VOCs and even self-adhered sheets for select roof system designs. The assembled membrane system is held in place on a roof by either adhering or mechanically attaching the base sheet.
A common and critically successful aspect of BUR and MB systems is their multiple layers. By installing a system with multiple layers, the effect of any slight vagaries that may occur during the application of each individual layer are diminished, resulting in a finished or complete roof membrane that performs as intended. Additionally, there is a synergistic strengthening aspect of multiple layers, each contributing to an incredibly durable and resilient roof covering.
For any roof system to be durable, resilient, and ultimately sustainable, it needs to be installed properly. The best low-slope asphalt roofing products cannot perform as expected if not installed correctly. In this context, “correctly” refers to following proper roofing practices and adhering to the installation instructions provided by the membrane manufacturer.
Manufacturers provide written installation requirements for their roofing systems and typically offer hands-on training courses to professional contractors who take these courses and obtain manufacturer certification.
In 2018 the National Roofing Contractors Association (NRCA) launched ProCertification. According to Jared Ribble, NRCA Vice President – Certification, “The program enables member contractors to also earn not just a manufacturer-specific certification, but an overall certification in modified bitumen roof systems generally with designations in heat-welded (torch-applied), cold-applied, hot asphalt-applied, and self-adhering.
“These workers give building owners confidence that their roof is being installed by committed and competent professionals. Manufacturers are grateful because warranty claims are less likely from jobs completed with ProCertified workers, and installers are glad to finally be recognized for the committed professionals they are,” says Ribble.
Once installed, MB and BUR roofs are very low-maintenance, but shouldn’t be ignored. The roofing contractor can also assist with an annual or semi-annual inspection to attend to any small problems before they become big issues.
This gravel-surfaced mod bit roof lacked regular inspection, and now the roots from some intrusive weeds have become a problem.
“We’ve installed thousands of commercial roofs over the past 40 years. Established in 1983, ARI specializes in re-roofing occupied buildings in Florida using BUR and modified bitumen roof systems. ARI’s satisfied clients, especially those with condos and commercial buildings near the ocean, rely on asphalt roofs to protect their properties from extreme weather conditions,” says Rob Kornahrens, founder and president of Advanced Roofing Inc. (ARI). “Recently, our team inspected a healthcare manufacturing facility we re-roofed in 2013, the DePuy Synthes building in Palm Beach Gardens, which still looks great and performs well after 10 years. With regular maintenance, we help prolong the roof’s service life and help building owners meet their obligations necessary to maintain the manufacturer’s product warranty.”
Mod bit and BUR roofs can be specified for all building types and in all climates. Kornahrens uses the roofing system for the Florida heat while Doug Fishburn, president of Fishburn Building Sciences in Ontario, Canada, specifies asphalt roofing in Canada.
When asked about his experience with mod bit and BUR, he states, “We’ve specified BUR and modified bitumen roofs on everything from schools to laboratories to professional buildings and clinics,” says Fishburn. “They continue to comprise a good chunk of our business because they work, even in the harsh Canadian climate, and they’re very cost- competitive.”
Of course, peace-of-mind roof durability isn’t free. The cost for long-lasting asphalt roof membrane systems includes material costs, installation costs, and a moderate budget for ongoing inspection and maintenance. Although exact roof system life expectancies vary, since MB and BUR roof systems have been known for protecting buildings for many years, they have a reputation as a low life-cycle cost choice among roof covering options.
“The performance of the products has certainly evolved thanks to numerous innovations made over the years, which has led to enhanced reinforcement strength, optimized polymer chemistry, and improved system design,” says Husnu Kalkanoglu, technical projects director at SOPREMA. “As an industry, various representatives meet regularly at organizations such as ASTM International to create and refine product standards and test methodologies, which help ensure product suitability and long-term performance. Modified bitumen membranes that are regularly tested for compliance with these industry standards have proven to perform well in real-world applications.”
For large-scale tests of critical roof perils, many manufacturers request product evaluations with FM Approvals. Mr. David Alves, Senior Engineer at FM Approvals, says, “Manufacturers request FM Approvals’ programs for various types of roofing components to be tested in assemblies. The programs for roof systems include a variety of hazards, including wind, external flame spread, internal fire contribution, and impact testing, to name a few. The actual test samples are tailored to the needs of all types of current-day low- and steep-slope roofing systems. In addition, all facilities producing FM Approved products are required to have routine surveillance audits during which some critical products are sampled and sent to FM Approvals for analysis. Building owners should have confidence that when manufacturers develop new products that are FM Approved, they’re put through their paces here before they hit the market.”
In addition to the resilience, durability, and proven performance of low-slope asphalt roof systems, this product offers several other benefits and options, including:
As a commercial or industrial building owner or manager, facility managers understand the important role a roof plays in ensuring the resilience of the building and the safety and comfort of its occupants. For this reason, low-slope asphalt roof systems, whether layers of traditional built-up roofing sheets and asphalt or modified bitumen membranes, can meet the challenge. These systems have a track record of millions of successful installations, providing exceptionally durable and resilient roof coverings while delivering the long-term, low-maintenance performance that building managers value and rely on.
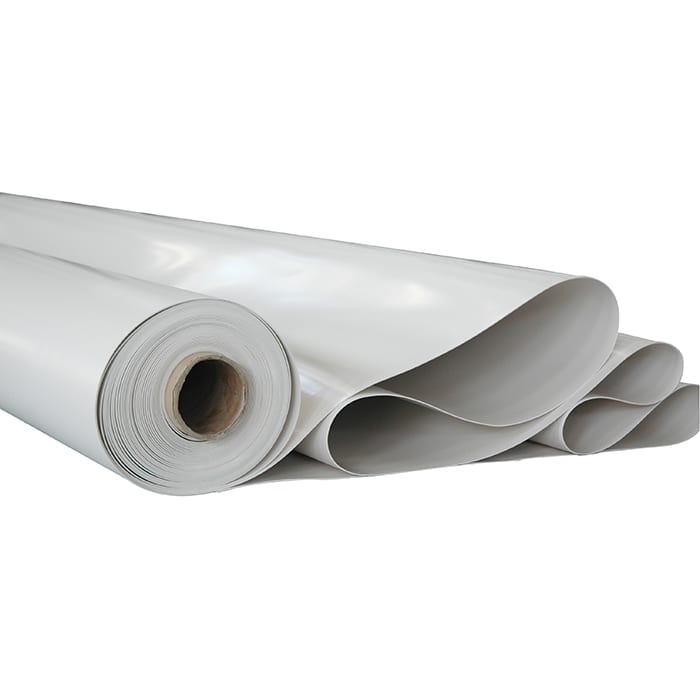
Acrylic Waterproof Coating To learn more about low-slope asphalt roofing systems, visit the ARMA website at www.asphaltroofing.org. Resource materials, award-winning project profiles, educational technical bulletins, and links to manufacturing member companies that offer extensive project profiles and product information are available. The ARMA Modified Bitumen Design Guide for Building Owners is an excellent resource for those involved in commercial real estate, as it contains a comprehensive summary of all aspects of modified bitumen roofing systems.