Online Robotics Trade Magazine Industrial Automation, Robots and Unmanned Vehicles
If you do not have a RoboticsTomorrow partner account, please register - it's free! Material Transfer Vehicle
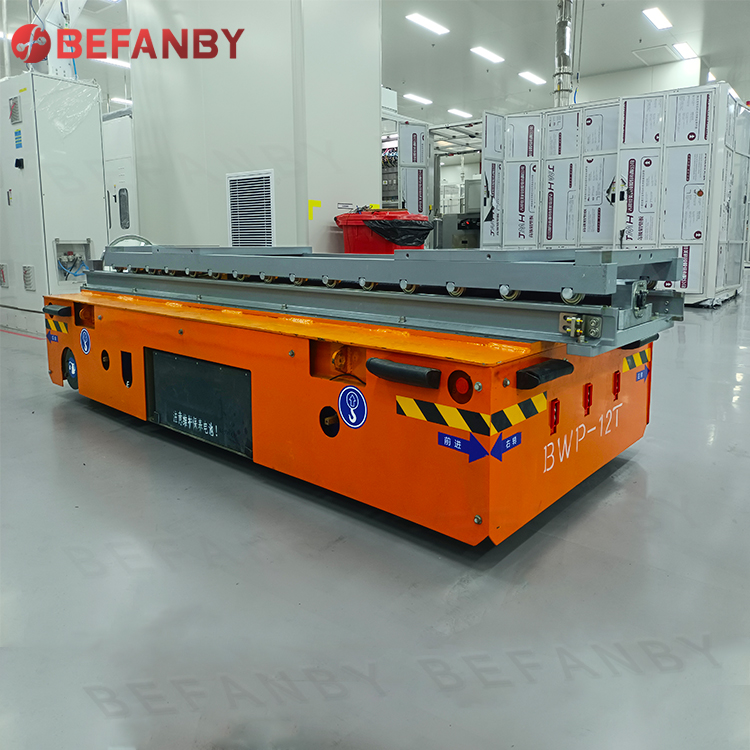
To enable the industry to keep pace with trends through quick and cost-efficient development, Markus Fenn and Prof. Dr. Stefan May developed Eduard, a teaching and prototyping platform that can be used to map current trends.
Q&A with Markus Fenn and Prof. Dr. Stefan May | Faulhaber
Industry 4.0 and Intralogistics 4.0. change the production environment and thus impact AGVs (Automated Guided Vehicles) and AMRs (Autonomous Mobile Robots). To enable the industry to keep pace with trends through quick and cost-efficient development, Markus Fenn and Prof. Dr. Stefan May developed Eduard, a teaching and prototyping platform that can be used to map current trends.
Markus Fenn: The robot itself is called Eduard, he's about 40 x 40 x 15 cm in size and weighs almost 8 kg. He is the result of a company making an inquiry with Prof. Stefan May. The company needed a platform to educate and train their employees on mobile robotics. That is why EduArt Robotik GmbH also comes with a range of teaching and service offerings for testing and optimization, in addition to the robot platform.
The platform offers simple rubber tires as well as mecanum wheels. These allow the robot to turn on the spot, drive sideways or diagonally. This enables exact positioning and navigation in very tight spaces. The rubber tires are mainly used for testing in outdoor areas or in rescue robotics, but only in pretend scenarios. The use of high-quality FAULHABER motors is ideal for both applications.
Markus Fenn: The platform has open interfaces, an integrated sensor concept with integrated distance and inertial measuring devices, and an integrated battery management system (BMS). This basic equipment can be expanded at the customer's request, either by us or the customer himself. This allows the customer to, e.g., select the gear ratio of the drive, whether 72:1 or 89:1, depending on the speed or torque required. This enables the customer to cost-efficiently test his new concepts. But we are also helping with the implementation of application solutions.
Markus Fenn: AGV and AMR are becoming more and more important for automation, but unfortunately companies are largely uninformed. The robot platform, for example, makes it possible to quickly and easily test a new sensor system. And because the platform can virtually be expanded as needed, it can bring the relevant knowledge into production.
Markus Fenn: AGVs and AMRs have the VDA5050 standard interface and can thus also communicate with the control center. Customers can easily test new software using a platform like Eduard, and the results can then be transferred 1:1 to large AGVs and AMRs. Applications can thus be evaluated without much simulation, because the software essentially remains the same, whether with Eduard or with a large system. A digital twin helps with the planning and expansion and is available with the platform on request.
Markus Fenn: For our training and PoC platform, we use DC-micromotors with precious metal commutation from FAULHABER. Despite their small size, they can generate a large amount of torque and are particularly power-efficient. They are also easy to control and are suitable for high-precision control loops.
For larger platforms, we use large DC-motors from the same manufacturer to enable a quick proof of concept, e.g., an easy controllability with your own electronics. If necessary, we then replace these with BLDC motors for the application, as these are maintenance-free and durable.
Markus Fenn: You need robots for smaller loads, i.e., smaller robots with smaller but more powerful drives, like the high-quality drives from FAULHABER. These autonomous industrial trucks have fewer electronics and smaller batteries, which means lower weight and decreased energy consumption. If the loads get higher again, it is easy to scale up and work as a unit, as the robots are able to work together collision-free thanks to high-precision drives.
Markus Fenn: When it comes to AGVs and AMRs, only the software is complex. What is important is the planning, so that the AGVs can work together seamlessly. To ensure that they not only recognize pallets, but also see whether they are full or empty or perhaps tilted, the AGV must be as intelligent as possible. This is where AI (Artificial Intelligence) comes into play. The complexity increases through the use of AI, and our small robot is ideal for testing this efficiently.
Markus Fenn: For this the robots have to interact with each other, 'think' themselves, exchange information via standard interfaces and, if necessary, cooperate. Whether the AGV/AMR is small or large, the software is essentially the same, the difference in the programs is only a few lines. The software only needs little information about the AMR. For example, it has to calculate where the robot is located on the hall plan. The navigation, which is one of the few components that knows the dimensions of the robot, then searches for the appropriate path. However, testing is always important because mobile robotics is in its infancy, which is why there are not that many standards yet.
In order to reach the required speed, the motor controller calculates the number of wheel revolutions required. Adjusting this takes three lines of code or a configuration file. FAULHABER supplies motors with high-precision gearheads and encoders for precise positioning, and together they provide optimum performance and safety.
Markus Fenn: Depending on the manufacturer, the systems can be made "unhackable" to a certain extent by separating the hardware from the Internet. Robots have safety scanners with distance sensors so they don't hit the wall. This means that even if hacked, the robot cannot perform any dangerous movements. And the process data is as secure in the network as the company network itself.
Markus Fenn: This takes place via 5G or via the company's internal WLAN. The systems do not need the data in real time because the data from the planning phase is available, for example the routes and speeds are available in the system in the route planning and do not change continuously. If the robot moves from one point to the next, a sign of life every few seconds is all it takes. So there's less data traffic in order not to overload the networks. The data itself is merged on the AMR and evaluated there. Encoders record what is happening and ensure safe control with the controllers.
Markus Fenn: Very safe. If one of four motors fails, the motor controller recognizes it and stops the drive. If a person enters the driving area, this is recognized by the laser scanner and the system brakes. These two security levels are enough.
Markus Fenn: Robots need to be better networked with each other. For example, four robots work together on a transport task, according to the motto: many smaller robots instead of one large one. For this you need a greater number of smaller motors that have to work with absolute precision, otherwise the robot swarm will stumble or lose its synchronization. In order to improve reliability, encoders must be absolutely immune to interference so that robots are not influenced by external interferences. For this reason, FAULHABER sometimes uses two encoders on each motor.
If you take the different gearhead variants from FAULHABER with their different lengths and diameters, together with encoders, controllers, etc., you can mathematically generate 25 million combinations, a considerable number of which have already been implemented at FAULHABER. This means that every company can find the optimal drives, also for future applications.
About FAULHABER FAULHABER is specialized in the development, production and deployment of high-precision miniaturized and miniature drive systems, servo components and drive electronics with up to 200 watts of output power. This includes putting into effect customer-specific packaged solutions as well as an extensive range of standard products, such as Brushless Motors, DC-Micromotors, Encoders and Motion Controllers. The FAULHABER trademark is recognised worldwide as a symbol of high quality and reliability in complex and demanding application areas, such as medical technology, factory automation, precision optics, telecommunications, aviation and aerospace, and robotics. From the powerful DC-motor with a continuous torque of 200 mNm to the filigree micro drive with an outer diameter of 1.9 mm, the FAULHABER standard range can be combined in more than 25 million different ways to create the optimum drive system for a particular application. At the same time, this technological construction kit is the basis for modifications which allow to configure special versions to meet the specific needs of customers.
Since 1961, FAULHABER MICROMO has partnered with OEMs to deliver high precision, high performance, custom micro motion system solutions to markets such as medical, robotics and automation in North America. FAULHABER MICROMO's tradition of innovation started decades ago in Germany. The groundbreaking invention of the FAULHABER coreless winding started it all for a market that produces millions of motors today. How can the FAULHABER MICROMO team help you deliver your next innovation to market first? Learn more about MICROMO's solutions for the most demanding applications, our diverse motion products and technologies, online ordering, Engineering and R&D teams, Clean Room Assembly, Machining Center and other services at our Clearwater, FL facility at https://www.faulhaber.com.
This post does not have any comments. Be the first to leave a comment below.
You must be logged in before you can post a comment. Login now.
Averting Factory Fires, Diminishing Downtime: How Thermal Imaging is Safeguarding International Production Lines
Advanced Ground Robotics Need Advanced Networking Solutions
Embracing a Purpose Built AIML System in Robotics
Navigating the Shift: Industry 4.0 vs. Industry 5.0 – Welcoming the Next Wave of Innovation
Enhancing Operational Safety: Cyber-Resilient Approaches for Physically Secure PCB Designs
Subscribe | Search | Promote Products | Feature Your Company | Publish News | List Event
Articles | News | Stories | Products | Companies | Events
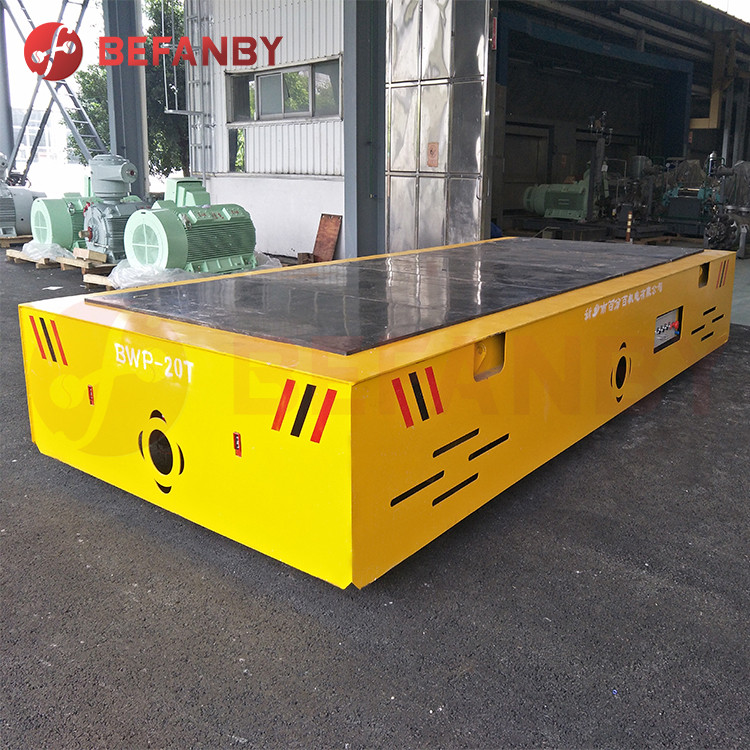
Electric Transfer Car © 2010 - 2024 RoboticsTomorrow - All Rights Reserved Powered by BTH Management