Keeping dust and debris out of the air is critical to protect personnel, production process, and equipment.
Dale Price, president, M&P Air Components Inc. Vibratory Separator
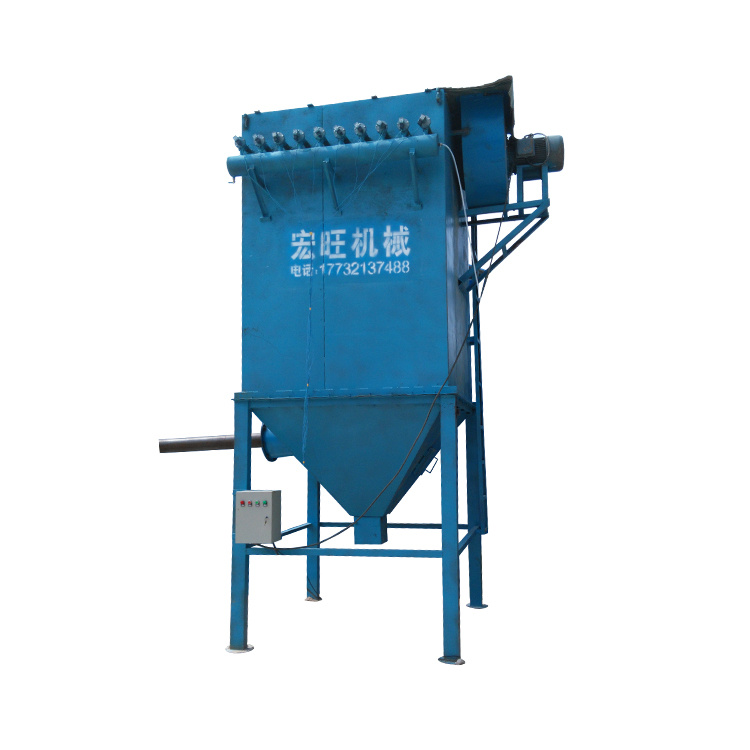
Effectively removing dust and debris from the air is a critical consideration for any industrial application. This is because airborne particles can pose health and safety risks to personnel, degrade or damage equipment or the surrounding environment, and interfere with production processes. This article explains the four primary types of dry dust collectors and how to choose the appropriate technology for your application.
The best dust collection method for your application will depend on airstream characteristics, contaminant characteristics (particle size, moisture, etc.), environmental factors, and efficiency and regulatory requirements. For the purposes of this article, we will focus on dry dust collectors, the four primary types of dry dust collectors, and how to choose the right method for your application.
Dry dust collectors are commonly used in industrial applications to remove dust, smoke, and fumes from a contaminated airstream using cleanable filters. In general, dry dust collectors are used for “friendly” dust that is free from oils and contains little moisture (note that dry dust collectors can successfully be applied to high moisture laden airstreams if the moisture is kept in a vapor phase while passing through the collector).
Dry dust collectors can be classified as either dry mechanical or dry media collectors.
* Dry Mechanical Collectors - The most common type of dry mechanical collector is a cyclone, which is often used as a pre-cleaner for other dust collection methods. Like many household vacuum cleaners, cyclone dust collectors use rotational velocity to generate centrifugal force that separates dust and debris from the air stream. The rapid circular motion thrusts debris to the wall of the cyclone. Once separated from the airstream, the dust particles fall into a hopper below, and the cleaned air exits the cyclone.
* Dry Media Collectors - Dry media collectors use a variety of different media to filter contaminates from the airstream. The most common types of dry media collectors are baghouse and cartridge dust collectors. Baghouse collectors will intake dirty air using long fabric tubes (bags) to capture dust on the inside or outside of the bags, and periodically clean the dust from the bags to capture the dust for reclaim or disposal while allowing cleaned air to exit the collector.
Cartridge dust collectors operate in a similar manner, but they leverage pleated cartridges to capture debris instead of bags. While many different media are used to suit specific application requirements, polyester bags are most common for pulse-jet baghouses and a cellulose blend media substrate combined with a surface loading treatment is most common for pulse-jet cartridge collectors.
Dry mechanical (cyclone) collectors are normally limited to removing dust in the 5-10-micron range and larger, while dry media collectors can be used for a wide range of dust, smoke, and fume applications with sub-micron contaminants. Cyclones are adaptable to a wide range of airstream temperatures, while baghouses are normally used for airstreams up to 500°F and cartridge collectors to about 275°F.
A reverse air collector is a type of dry media baghouse dust collector. Bags of fabric are hung and tensioned inside of the dust collection unit. As dirty air flows into the unit, debris is captured on the inside surface of the bag, while clean air exits through the bag. The unit is cleaned at regular intervals, or once the dust load of the bags reaches a defined threshold.
To clean the bags, a fan blows clean air in the reverse direction, causing the accumulated dust in the bag to break apart and release from the fabric and fall into a hopper below. Because the cleaning process for reverse air collectors must be done offline, a redundant unit is required to ensure continuous dust collection.
Reverse air collectors are most commonly used for high-volume, high-temperature dust collection applications (i.e. power plants and utilities). The technology was prominent through the early 80s, but it has lost some of its appeal due to the adoption of newer technologies and the prohibitive added costs of owning and maintaining redundant units. A pulse jet baghouse dust collector for continuous duty with high entry inlet and explosion protection vent panels
A pulse jet collector is a dry media collector that uses either bags or cartridges to collect dust and debris from the airstream. A key difference between pulse jet collectors and reverse air collectors is that debris accumulates on the outside surface of the bag or cartridge in pulse jet collectors.
In addition, pulse jet collectors have air-electrical cleaning systems that use compressed air to clean the filters. Compressed air is pulsed into the top of the filter at 80-100 psig for 0.1 to 0.3 seconds. As primary air enters the filter, secondary air is induced from the clean air plenum and combined with primary air to reverse the flow of air in the filter element. The reverse flow of air forms a bubble in the top of the filter traveling down its length, restructuring the dust cake, and discharging dust into the hopper.
With pulse jet collectors cleaning can be done while the unit is online, so the system does not require redundant units for continuous operation. Cleaning can be done on either a timed cleaning schedule or on demand. In a timed schedule, the cleaning action is activated on a continuous timing cycle, which offers simple control and ensures that the unit will always be cleaned when on. However, timed cleaning cycles reduce filter life and use a large amount of compressed air. On-demand cleaning activates when the media differential pressure exceeds a predetermined threshold. This enables longer filter life and lower compressed air usage. Cartridge-Type Pulse Jet Collectors
Cartridge-type pulse jet collectors are now by population the most common type of collector for industrial manufacturing. The popularity of cartridge pulse jet collectors is largely due to the high filtration efficiency, lower capital cost, smaller size, and greater flexibility of its modular construction compared to alternative methods.
Cartridge collectors are side-loaded for flexible installation and maintenance. However, cartridges have their limitations. They are best suited for collecting dry, non-abrasive dusts and handling moderate dust loads (around 2 gr/cu ft). Cartridges are not normally used in applications where the airstream temperature exceeds 275°F, or for dust that contains oils or sticky substances that can adhere to the pleats of the cartridge; these applications tend to favor baghouse or wet collectors.
Pulse jet baghouse collectors offer some of the most versatile designs and are well suited for the widest range of industrial applications. Baghouses adapt well to high temperatures and non-standard gas applications and are generally more forgiving than cartridge collectors. A reverse air baghouse dust collector for continuous duty handling high particulate loadings exhausting filtered air to the atmosphere
Reverse jet dry dust collectors, also known as reverse jet baghouses, are a hybrid of the pulse jet collectors and cyclone methods. Reverse jet baghouses use positive displacement blowers or high-pressure fans to continuously blow air into the unit and clean the unit while it is online, eliminating the need for redundant units. These collectors are an energy-saving alternative to other high-volume dust collection methods, while offering comparable performance. Parallel cyclones separating particulate from the airstream and exhausting cleaned air to the atmosphere
Finally, cyclones are a dry mechanical form of dust collection and can be used either as a pre-cleaner to a secondary collector or as a final collector. When used as a pre-cleaner, the cyclone’s purpose is to either 1) remove contaminants from the airstream which might be detrimental to the performance or function of the secondary collector or 2) to reclaim high-value contaminants from the airstream for process recovery or re-use. When used as a final collector, the cyclone is customized for its geometry and performance to match specific contaminant and process characteristics and can achieve the same final efficiencies as a dry media collector.
Keeping dust and debris out of the air is critical to protecting the health and safety of personnel, maintaining the integrity of your production process, and extending the life of your equipment. However, choosing the right dust collection methods requires a close examination of a wide range of factors--from dust and airstream characteristics to energy efficiency requirements and installation constraints. Partnering with a knowledgeable and experienced dust collection and air handling equipment manufacturer can help you identify the appropriate solution for your application.
Dale Price is president of M&P Air Components Inc. (Huntington Beach, CA), serving as a New York Blower’s representative for industrial fans in Southern California. Price has 38 years of experience in the design and application of dust collectors and industrial fan applications.
Mars to Invest $230 Million in Nature's Bakery Facility
Kellanova Names New President, Other Leadership Changes
EPA Fines Chemical Wholesaler for Inaccurate Reporting
Suspected Acid Explosion at Mining Supply Company

Magnetic Separation Copyright © 2024 All rights reserved. Informa Markets, a trading division of Informa PLC.