New and efficient approaches to cabinet and console design, fabrication, integration, and qualification are enabling prime defense contractors to quickly equip the U.S. Navy with better electronics technology and enclosures while increasing return on investment. As the Navy adds new mission capabilities and refreshes existing ones, the protective cabinets and consoles that house these critical systems are increasingly leveraging innovative design, production, qualification, and integration solutions to deliver more functionality while making them easier to deploy and maintain.
The cabinets and consoles that house shipboard mission electronics, processing, storage, connectivity, and human/machine interfaces (displays and workstations) must be able to protect mission systems from damp heat, saline atmosphere, shock, vibration, and electromagnetic interference (EMI) while maintaining secure and efficient cooling for long-term reliability. Although these enclosures are critical for mission success, their design and manufacture can place unwanted demands on the already limited resources of the companies who could supply both the enclosures and electronic payload. Low Voltage Power Distribution Cabinet
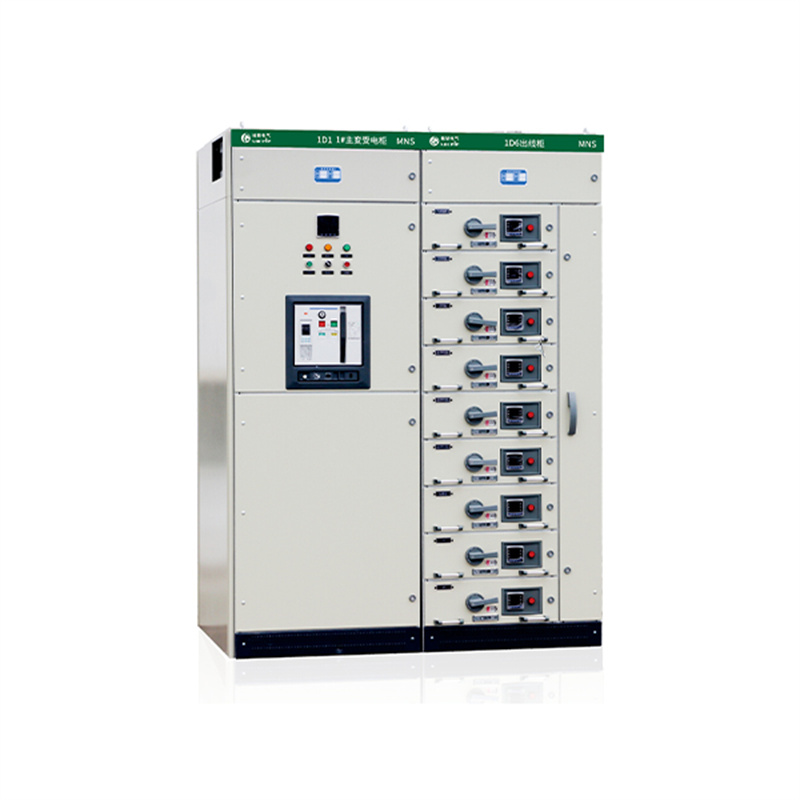
The result: Design and production of shipboard enclosures is transitioning from the prime contractors over to dedicated enclosure producers that can seamlessly augment the primes’ contractor capabilities with the expertise required to produce quality built-for-purpose enclosures. By taking on the prime contractors’ burden of designing, manufacturing, qualifying, and integrating shipboard electronics enclosures, these vendors create an efficient, low-risk alternative source that enables the prime contractor to instead focus on their primary sources of value creation.
Naval-enclosure vendors, leveraging commercial off-the-shelf (COTS) technology and a modular approach to equipment enclosure construction and payload integration, can enable more vertical-integration capability, design maneuverability, better affordability, and simultaneously lower technology and schedule risk. Affordability and risk reduction are further boosted with proven technology building blocks that enable faster development of purpose-built solutions for new programs.
This kind of “one-stop-shop” for complete integrated equipment enclosure solutions – one that addresses the complete technology chain from specification requirements to delivery of fully qualified equipment – drives program value while further reducing risk.
Let’s do an overview of the design considerations required for naval enclosures. (Figure 1.)
[Figure 1 ǀ The cabinets and consoles that house shipboard mission electronics, processing, storage, connectivity, and displays/workstations) must be able to protect mission systems while maintaining secure and efficient cooling for long-term reliability. Image: Curtiss-Wright.]
Qualification of naval enclosures can be expensive, especially regarding the schedule impact if the equipment under test fails and needs to be re-engineered. High-impact shock qualification (per MIL-DTL-901) using COTS payload equipment is often identified as a program risk. Because of this factor, the assurance of qualification approval is critical. The best way to de-risk shock testing is with a robust engineering phase that assesses system rigidity and reduces equipment shock impact to ensure system survivability. What does this mean? It means that naval-enclosure vendors must have engineering and test teams with deep electromechanical, shock, and vibration expertise across many naval programs.
Depending upon the electronics payload, vendors may use MIL-M-17185 and MIL-PRF-32407 (both addressing resilient mounting) standards for approved isolation mounts to mitigate the risk of shock test failure. In-house modeling capabilities, performed during the design phase of the project, can ensure qualification testing success with no program delays. Those who need such equipment should look for COTS vendors whose testing capabilities include acoustic, shock, vibration, environmental, emissions testing, and qualification.
IPC-A-620 and J-STD-001 (addressing connection and solder) certified operators are required to perform both power distribution and payload wiring. Wire crimping and soldering should be assured by trained assembly technicians. Automated test equipment performs point-to-point electrical verification (continuity, dielectric strength, and insulation resistance per IPC-A-620 or MIL-STD-202), while fiber-optic cable testing should be performed to MIL-STD-2042 per qualified technicians.
Flat-panel displays (FPD) are the human-machine interface required on a vessel for equipment operation and monitoring. These displays are ruggedized and reliable while offering the highest color fidelity in all conditions over extended periods. Vendors should work with industry-leading embedded display partners to create an FPD specification that meets or exceeds the system’s functional specification requirements for reliability and performance.
If possible, the vendor should procure, validate, and integrate FPDs using in-house produced cabling and interfaces to offer a higher level of turnkey integration. Other qualified suppliers provide keyboards, trackballs, and joysticks that are similarly integrated. The interface between the user and the equipment must be carefully considered to remain mission-focused, following the guidelines of MIL-STD-1472 and ASTM-F1166 (human-engineering design criteria).
Naval enclosures should be built from the ground up, using components and assembly approaches that are intended to meet or exceed the requirements of MIL-DTL-901 (shock) and MIL-STD-167 (vibration) for mission-critical Navy shipboard applications, plus other MIL-STD-810 environmental requirements. Leading enclosure vendors have extensive in-house thermal, structural, environmental, and electromagnetic interference and compatibility engineering expertise gained over hundreds of naval programs, and are able to systematically identify and mitigate the technical risks associated with a new functional specification.
Enclosures need to be designed and built to offer exceptional environmental protection from liquid and other contaminant ingression and EMI and must limit acoustic noise emissions. For example, enclosures and integrated systems should be designed, built, and tested for compliance with MIL-STD-108 and MIL-STD-810 for drip, heat, and humidity environmental protection; MIL-STD-461 for EMI compliance; and MIL-STD-740 and MIL-STD-1474 for acoustic noise generation, among others.
Engineered for ease of use
For naval enclosures, the use of common building blocks adds additional functionality while lowering technology risk and cost. The philosophy of this design approach is seen in the use of standard tools for maintenance, use of captive fasteners that can be moved and replaced, removable doors and panels that can hinge left or right, extension slides for full payload equipment access, and easy-to-reroute and quick-disconnect cable and power distribution harnesses. This approach also reduces maintenance complexity, keeping system downtime to a minimum.
Due to their size and weight, U.S. Navy ruggedized enclosures do not easily fit through a ship’s hatch. Cutting and removing portions of a ship’s infrastructure is a common practice required to maneuver and install equipment enclosures above and below decks. Besides significant cost increases and schedule delays, shipboard enclosure installations are one of the leading causes of Navy shipyard injuries during a vessel’s maintenance period. For those reasons, enclosure and system solutions should be purposely built to mitigate these high risks through modularity and hatchability. (Figure 2.)
[Figure 2 ǀ Modular construction of enclosures and systems solutions enables additional design and installation maneuverability.]
Designs considering modularity and hatchability also add significant program design and installation maneuverability. Modularity aids rapid solution development and reduces risk by leveraging proven reusable technology blocks with standard interfaces designed for easy disassembly and reassembly. Hatchability – the ability to move enclosures, their payload components, and cooling and power distribution systems through hatches without cutting bulkhead holes and quickly reassemble them where they are required – is a significant cost-saver for contractors.
A key feature of modularity involves the use of cable ladders: This cable-routing approach enables removal of wire-harness assemblies from the enclosure without the complexity of undressing the cables and wiring; the cable ladders can be safely removed from the enclosure with the harness remaining intact and secured. Upon passage through hatches, harnesses are easily reinserted into the cabinet, and are then connected to the payload and enclosure’s connector panels.
This modular construction approach enables system hardware upgrades as necessary and is not dependent on a hull work schedule.
Naval enclosures are designed to protect heat-generating electronics from humidity, ambient heat, saline atmosphere, and other contaminants, requiring them to be sealed. Dissipating electronics’ heat for long, reliable system operation requires careful consideration of the enclosure’s payload, installation environment, and cooling resources available. To address the cooling situation, solutions may be passive (convection and/or conduction), forced-air, liquid (water or refrigerant), or a hybrid of several cooling schemes.
Power delivery, conversion, conditioning, distribution, and electrical isolation of payload equipment are critical functions of all naval equipment enclosures. Power requirements must be customized to specific equipment enclosure configurations. Ideally, the COTS naval enclosure designer should offer an ecosystem of interoperable technology building blocks optimized for efficient enclosure integration of custom power distribution systems, with compliance to MIL-STD-1399/300 (addressing Navy voltage systems), among other considerations.
Enclosures may be equipped with single or redundant power sources and integrated with any power conversion. In addition, an uninterruptable power supply (UPS) may be required by the functional specification. The UPS approach uses power modules that assure power stability through a transfer switch between two separate sources of supply for continuous power availability and quality; an auctioneering feature selects the most stable of the two sources. For single-source power supplies, battery packs installed in the enclosure or positioned remotely ensure that the payload remains operational throughout power shortages.
While battery technology is evolving quickly, traditional lead-acid banks remain the common choice onboard ship. However, well-established characteristics aside, lead-acid batteries are heavy and space-hungry. As the NAVSEA/NSWCCD [Naval Sea Systems Command/Naval Surface Warfare Center, Carderock Division] assesses lithium iron phosphate (LiFePO4) batteries for naval use, that technology is available to Navy programs, using best-in-class commercial products that offer significant reliability, power density, and extended life benefits to further demonstrate the viability of the new battery chemistry.
Fred Sainclivier is Senior Engineering Manager, 901D, Curtiss-Wright Defense Solutions
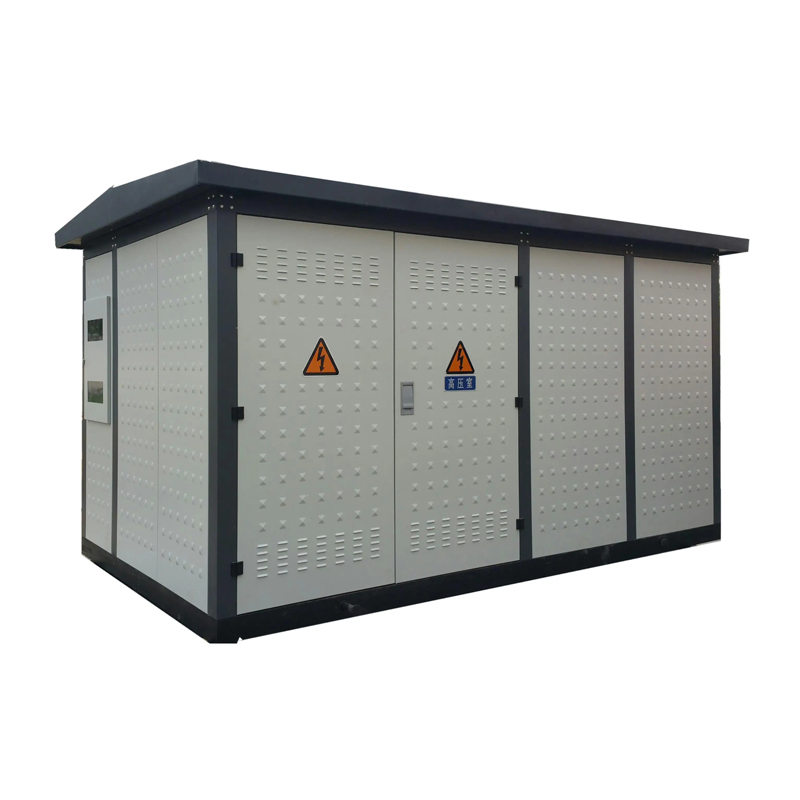
Switchgear Curtiss-Wright Defense Solutions https://www.curtisswrightds.com/