We use cookies to enhance your experience. By continuing to browse this site you agree to our use of cookies. More info.
From underwater surveillance vehicles and deep-diving construction engineers to paddle-boarders and surfers, users of polyurethane foams fulfill diverse subsea and marine applications. Polyurethane Foam For Mold Making
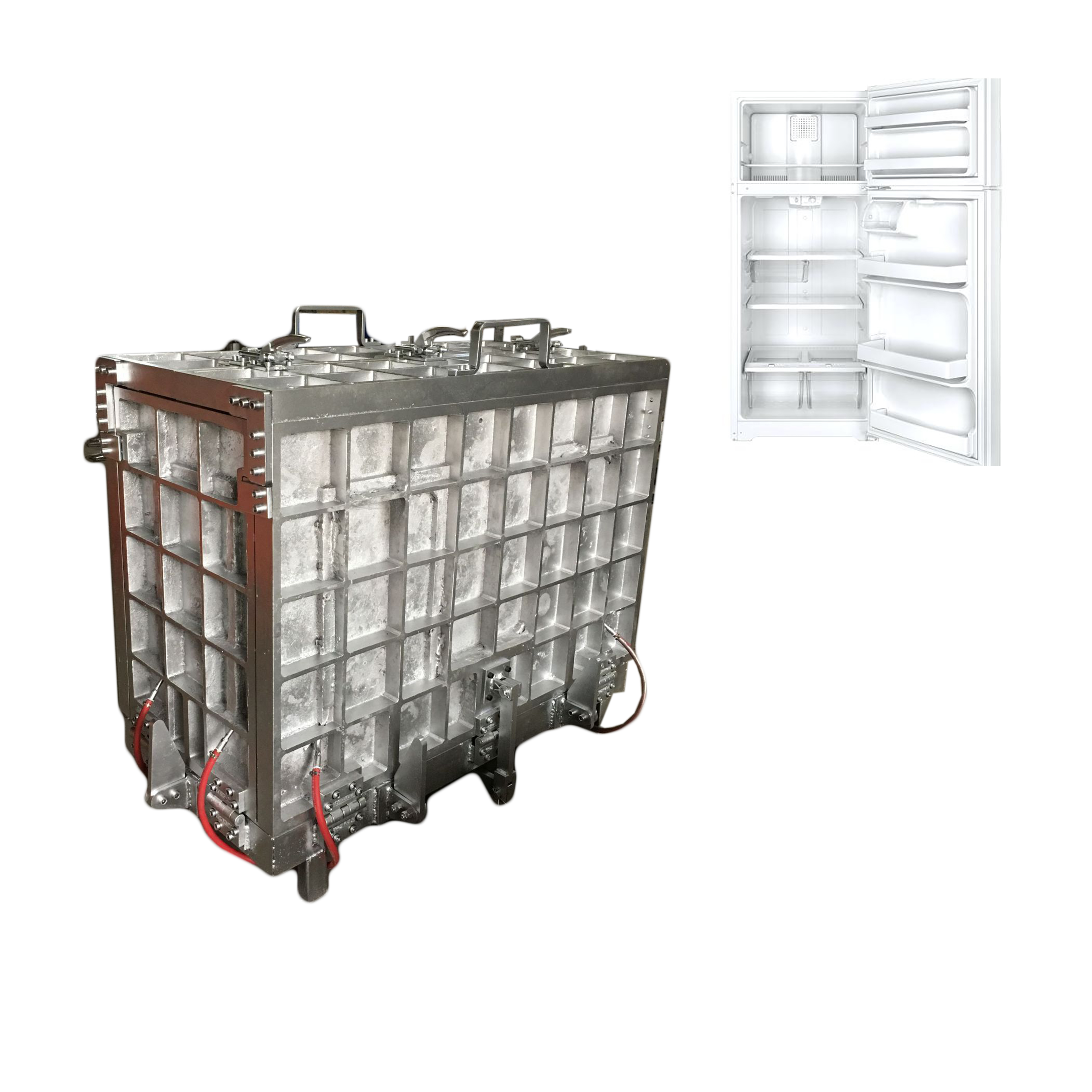
Thanks to their unique chemical and physical properties, General Plastics’ specially formulated polyurethane foams outperform wood and other materials while ensuring to address the specified challenges.
Image Credit: General Plastics Manufacturing
A Hollywood studio’s special effects team recently enlisted the assistance of General Plastics for an underwater project. The studio sought to capture the true motion of sharks and other aquatic animals in their natural settings rather than relying on green-screen technology or computer-generated imagery (CGI).
The special effects team created a mini rig that used timed-release adhesive to adhere to the dorsal fins of these fish and marine mammals. The rigs were waterproof and had a small high-definition camera and GPS transmitter. The fish would be released into rivers, streams, and shallow beaches after being fitted with the device.
After a given amount of time, the rigs would detach from the fish and float to the surface. Following GPS directions to their surfaced location, studio personnel would collect the rigs and use the footage in their movies.
The special effects team needed to bond the rig to a water-resistant, lightweight material that could accommodate various depths of water. In order to retrieve the rigs, the material also needed to be able to float the rigs up to the surface of the water once released from the dorsal fins.
Based on its closed-cell characteristics and flotation properties, General Plastics' subsea foam was ideal for this project.
We worked with our customer to identify the right density based on the weights of the rig, camera, and GPS transmitter, as well as appropriate sealants and adhesives.
Geoff Veld, Senior Business Development Manager, General Plastics Manufacturing
All of the different adhesives that the studio team had previously used or deemed acceptable were compatible with General Plastics' materials, and the finished material was machined at General Plastics, meeting the customer’s specifications. When it arrived, it was ready to bond and needed no additional post-processing.
A far denser syntactic substance would have been the only other flotation choice for shallow-water applications. According to Veld, that would have been overkill because it is meant for application hundreds or thousands of feet below the surface line and is less buoyant due to its density.
Furthermore, because of the glass/ceramic bead fillers that allow them to keep their strength at such high pressures, syntactic foams are significantly more difficult to manufacture and may cause the machining bits to excessively wear.
If you’re used to running foam or wood, and you jump straight to syntactic foam as flotation material, there’s a big learning curve in understanding how to keep your machining bits from breaking.
Geoff Veld, Senior Business Development Manager, General Plastics Manufacturing
In applications like underwater construction, the R-3300 subsea foams help keep materials floating at a specified level. Those building floating bridges or working on oil rigs can keep their tools within arm’s length because the foam creates a near-weightless effect.
It keeps the tools from floating to the surface or sinking if they are heavier. Some divers utilize the foams to make a huge camera setup appear weightless underwater. They can also be used as a component of an automated remote-operated vehicle (ROV) that floats a camera through the water.
These foams are excellent for mapping or scanning underwater areas for general exploration, defense, or even treasure hunting.
Image Credit: General Plastics Manufacturing
In addition, the buoyancy material has been used in marine-themed educational projects. In the Marine Advanced Technology Education (MATE) competition in 2016, a student-built underwater ROV made of the LAST-A-FOAM® R-3315 foam won many international awards.
ROV competitions at the MATE Center encouraged students to develop and build underwater robots that were capable of handling real-world mission tasks. The foam was an important part of the team's ROV, which needed to produce enough buoyancy at the bottom of NASA’s 40-foot-deep Neutral Buoyancy Lab (NBL).
The Seattle-based group, which was largely made up of high school students, used calculations to establish the appropriate amount of flotation for their vehicle, which they then used to create a float that was installed on top of their ROV.
The team credited the subsea foam, as well as the technical assistance throughout the design process, for their success at NASA’s NBL and for contributing to the professional appearance of their ROV.
This subsea foam has been tested for performance down to 1,200 feet without coating and up to 2,400 feet with coating. The 12-pound density is often employed in relatively shallow applications or lightweight items.
When coated with polyurea or another layer of polyurethane, higher-density foams may withstand pressures in deeper waters, presumably doubling their hydrostatic pressure resistance.
These polyurethane foams are significantly superior to wooden floats or other materials that can be damaged or distorted by water, salt, and weather conditions in buoy-type applications. While water absorption is negligible and the foams are highly durable and rugged, researchers still advise the application of a coating to protect from UV energy for longevity
Providing value to clients extends beyond product creation and selection to process simplification. Previously, one of General Plastics’ boat-builder customers used a three- or four-step technique to create tooling molds.
They were making monolithic tooling to produce large shells for different hull designs. Essentially, they would cut one layer, measure it, add a putty or epoxy resin to the outside, and then add another layer of a slightly higher-density foam that could be used in conjunction with a fiberglass layup.
Geoff Veld, Senior Business Development Manager, General Plastics Manufacturing
The specialists at General Plastics examined the material cost, processing time, and impact on the consistency of the end product using smaller test models. The customer changed his opinion after learning about the benefits of employing a homogeneous molding solution.
They now use the LAST-A-FOAM® FR-4500 tooling material (12 and 30-pound densities) instead of three or four materials, saving them roughly 20% in time and 5% in overall cost. Instead of constructing a plug out of different foam materials for a layup, they manufacture their tools out of foam, bond it, sand it, and cut it to size, then lay it upright on the foam material.
Furthermore, because the polyurethane foam contains no abrasive fillers, it is easy to cut, fill, and sand. The product also readily accepts virtually any bonding agent or sealant. Customers appreciate the various available options that are available to help them acheive their desired value and surface finish.
A 30- or 40-pound material will require minimal sanding but will result in a much heavier tool, while a 12- to 15-pound density will result in a lighter product but will require more sanding to achieve the same finish.
In composite applications, a Washington-based yacht builder uses the rigid, flame-retardant LAST-A-FOAM® FR-6700 foam series as a wood replacement for its custom-designed ship interiors. Mid-priced materials with densities ranging from 15 to 25 pounds are utilized for everything from drawers, cabinets, and tabletops to moldings.
To offer a more appealing, finished appearance, the foam is either wrapped in fiberglass/resin or wrapped in decorative vinyl. As FR-6700 does not absorb salt water, it does not swell or distort like wood in a marine setting, giving a composite panel more dimensional stability and durability.
Image Credit: General Plastics Manufacturing
Polyurethane foams are ideal for water sports applications ranging from oars to surfboards. General Plastics assisted one customer in profitably expanding their product line. General Plastics' foam products have been used as core material for various paddle and oar designs over the years, but they wanted to broaden their offers by capitalizing on the popularity of stand-up paddle boards.
After testing five or six different wood, foam, and plastic core materials, the customer came to General Plastics for a better solution. Finally, they discovered that using the LAST-A-FOAM® FR-7100 Multi-Use Foam Series in four-pound density as the composite core material for their paddle boards offered the greatest value.
It provided the potential to optimize their profit by being a lightweight product with closed-cell features and at a lower cost than other wood alternatives.
As many stand-up paddle board products are wrapped in fiberglass, they often do not require a flotation-specific material like subsea foams.
In the case where LAST-A-FOAM® is used as core material, a fiberglass failure will have negligible impact on this board since it is a closed-cell foam. It will not absorb water or warp.
Moreover, the FR-7104 foam is much lighter than wood and more compatible with lay-up resins when compared to Styrene-based foam cores, making it easier to manufacture, resulting in a lighter board to transport and float.
This information has been sourced, reviewed and adapted from materials provided by General Plastics Manufacturing.
For more information on this source, please visit General Plastics Manufacturing.
Please use one of the following formats to cite this article in your essay, paper or report:
General Plastics Manufacturing. (2023, July 18). Using Polyurethane Foams in Subsea and Marine Applications. AZoM. Retrieved on January 01, 2024 from https://www.azom.com/article.aspx?ArticleID=22280.
General Plastics Manufacturing. "Using Polyurethane Foams in Subsea and Marine Applications". AZoM. 01 January 2024. <https://www.azom.com/article.aspx?ArticleID=22280>.
General Plastics Manufacturing. "Using Polyurethane Foams in Subsea and Marine Applications". AZoM. https://www.azom.com/article.aspx?ArticleID=22280. (accessed January 01, 2024).
General Plastics Manufacturing. 2023. Using Polyurethane Foams in Subsea and Marine Applications. AZoM, viewed 01 January 2024, https://www.azom.com/article.aspx?ArticleID=22280.
Do you have a question you'd like to ask regarding this article?
AZoM.com - An AZoNetwork Site
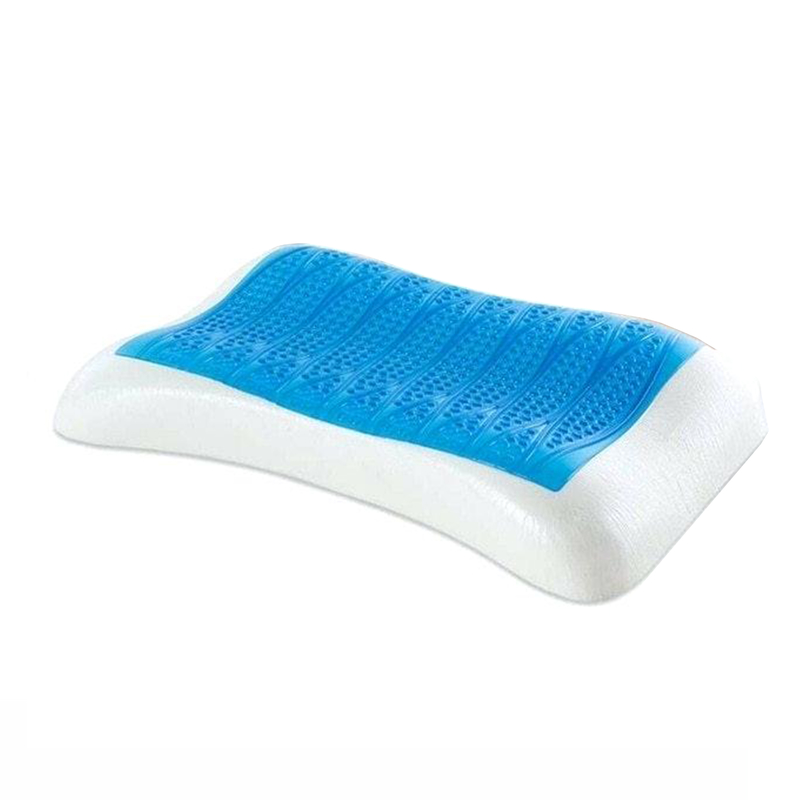
Poly Jacking Equipment Owned and operated by AZoNetwork, © 2000-2024