At the base of the Sphere at the Venetian Resort in Las Vegas is a 350,000-sq-ft “collar,” a curved concrete-framed structure topped with a compression ring that holds the larger structure in place.
In a city already filled with “one-of-a-kind” attractions, the newly opened Sphere at the Venetian Resort in Las Vegas has pushed the benchmark for “unique” even higher. Metal Slitting Machine
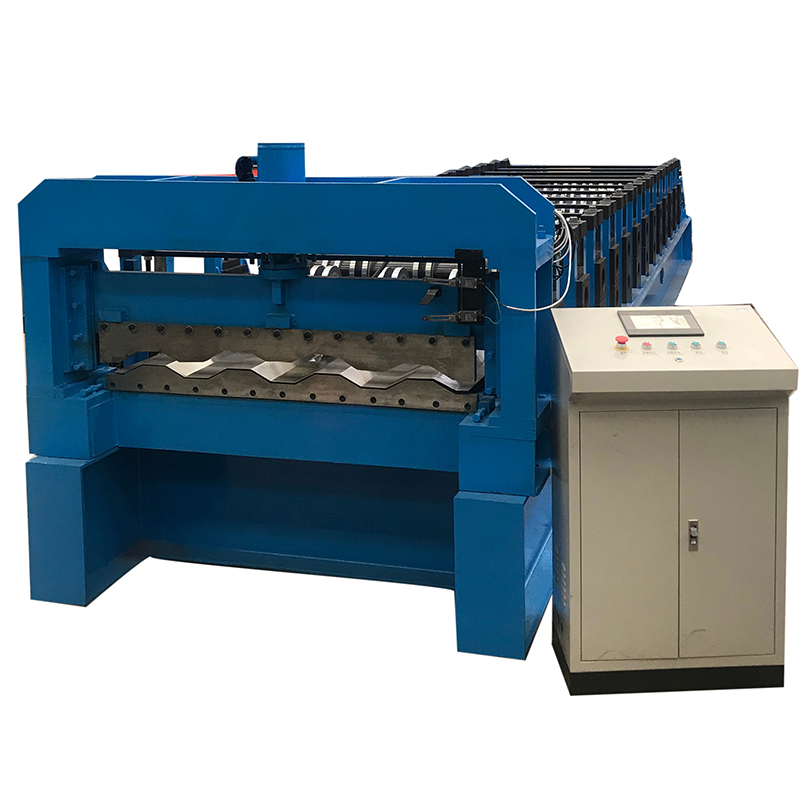
Measuring 366 ft high with a maximum width of 516 ft, the $2.3-billion entertainment venue is the world’s largest structural sphere. An outer “exosphere” fitted with a 580,000-sq-ft exterior LED display surrounds a domed 18,600-seat auditorium rich in immersive audio and visual technology, punctuated by a 160,000-sq-ft LED screen, the largest and highest resolution display of its type known to exist.
At its base, the Sphere is nearly completely wrapped by a two-floor, 350,000-sq-ft “collar,” a curved concrete-framed structure containing back- and front-of-house spaces. It is topped with a compression ring that holds the larger structure in place. The collar is clad with 32,000 sq ft of custom exterior finish insulation system (EFIS) panels manufactured and installed by specialty contractor KHS&S.
Measuring 366 ft high with a maximum width of 516 ft, the $2.3-billion entertainment venue is the world’s largest structural sphere. Photo courtesy KHS&S
Although it might at first appear to be a relatively routine part of the Sphere’s complex construction process, it was anything but, according to KHS&S area operations manager Brandon Kephart.
Characterizing the collar as “really more of a sculpture than a structure,” Kephart explains that the collar has a unique geometry all its own, varying in height from 16 to 38 ft, and the sweeping side is tilted at angles ranging from 5% to 35%. What’s more, other exterior trade work such as aluminum tracking and glazing placed over the EFIS was dependent on each panel’s exact positioning.
Much like designing, manufacturing and assembling a highly intricate puzzle, creating this unique, non-uniform shape with flat EFIS panels meant that none of the 142 trapezoidal units could be alike.
The collar is clad with 142 unique exterior finish insulation EFIS panels. Photo courtesy KHS&S
“Each one would have to be custom-designed, manufactured and installed to precise specifications,” says Kephart.
Applying some technological acumen of its own, the KHS&S team used multiple 3D building information modeling systems to calculate the unique geometry for each panel’s distinctive shape, which included unequal sides and angles. To maintain the collar’s curvature after being fitted with multiple layers of insulation, waterproofing and a finishing coat, the panels would vary in thickness from 7.5 in. to 10.5 in. Attaching the panels to the concrete frame would require more than 5,000 heavy-gauge clip anchors.
A leased temporary yard located approximately two miles from the Sphere project served as the hub of KHS&S’s four-step EFIS assembly line manufacturing operation. The panels’ metal stud kits, completed by a steel roll forming machine at the company’s main prefabrication facility in California, were assembled and layered in a process that had multiple quality control inspection points, with photo and checklist verification to ensure compliance with design tolerances.
Beginning with a 16-ft unit for the collar’s base, the panels were produced in the order in which they would be installed. A high visibility number affixed to each panel provided a further safeguard against mix-ups.
Approximately four to five panels were installed each night in the same order they were manufactured. Photo courtesy KHS&S
As storage space at the Sphere jobsite was limited, KHS&S shipped approximately five completed panels at a time aboard a custom semi-truck rack system. With a total station verifying each unit’s GPS-based positioning coordinates, a 40-ton crane hoisted panels into place. They were then anchored at the top, middle and bottom. As panel installation worked its way around the collar, the three-dimensional trajectory increased to the curved collar’s maximum height and tilt, then decreased in reverse order. Personal protective equipment and HEPA vacuums protected workers from the substantial amounts of silica dust generated by drilling the intricate gauge and bolting system.
Kephart says for all its complexities, the collar’s EFIS installation process went smoothly, albeit with a few last-minute challenges.
“The bottom of the panels are three-quarters of an inch above the sidewalk hardscape structures, which weren’t in place when we were doing the installation,” he explains. “Sometimes, some field adaptations were needed to make sure everything lined up as expected.”
KHS&S played a role in the Sphere’s interior appearance as well. Originally contracted to provide back-of-house painting, the scope was expanded to include all inside surfaces, totaling nearly 1.8 million sq ft of interior paint as well as installation of all wall coverings, custom vinyl graphics and several specialty plasters.
To access the most distant reaches of the Sphere’s curved walls and peaks, KHS&S coordinated with other trades to use a network of high-reach booms and specially engineered suspension scaffolding hung from the steel catwalk. A dedicated crew member was tasked to inspect the scaffolding system each day, while an interior wash station captured wastewater from painting and wall covering work for proper disposal. Despite the high-flying nature of the interior work, KHS&S’s painters matched their outdoor EFIS co-workers in achieving a perfect safety record as well as meeting their budget and scheduling targets.
In addition to schedule and pull planning, briefing stand-up boards and other lean construction practices, Kephart credits the Sphere’s teamwide collaboration for enabling KHS&S and other trades to successfully coordinate and carry out a host of intricate activities amid a crowded, bustling jobsite.
“It’s the nature of the Las Vegas market,” he says. “With many large complex projects and owners with exacting requirements, teamwork is critical.”
Yet even Kephart, a seasoned area construction veteran, has to admit that when it comes to the Sphere, “there’s nothing like it anywhere in the world.”
You must have JavaScript enabled to enjoy a limited number of articles over the next 30 days.
Top Design Firms Southwest Design Firms Report Robust Revenue Gains in 2022
Top Contractors Construction Staying Strong, But Labor Challenges Ahead
Top Specialty Contractors Southwest Specialty Contractors Thrive, Share Optimism for 2024
Copyright ©2024. All Rights Reserved BNP Media.
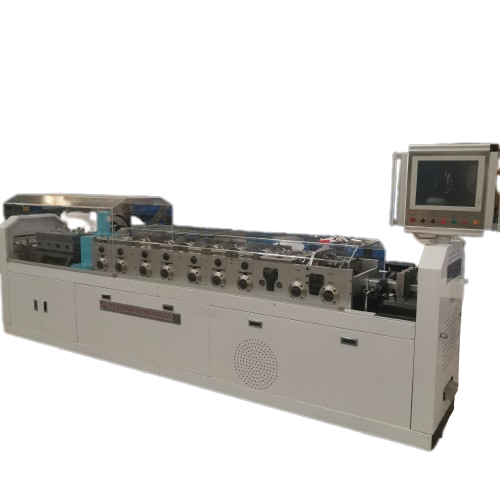
Color Steel Metal Glazed Tile Roll Forming Machine Design, CMS, Hosting & Web Development :: ePublishing