Tesla has pioneered the use of massive casting machines, also known as gigapresses, to make large single pieces of vehicle underbodies, streamline production, and reduce the work of robots. The company’s die cast — or gigacast, as Elon Musk calls it — will now think of the entire underbody of its EVs as a single piece. Let’s do a deep dive into gigacasting and learn what’s pushed it to the pinnacle of EV manufacturing.
How has the assembly line approach to electric vehicles hurt manufacturers? Tesla CEO Elon Musk has argued that legacy assembly processes have needed to be changed for battery-powered vehicles. He states that part of the problem is that assembly needs to be simpler and faster. Car Frame Machine
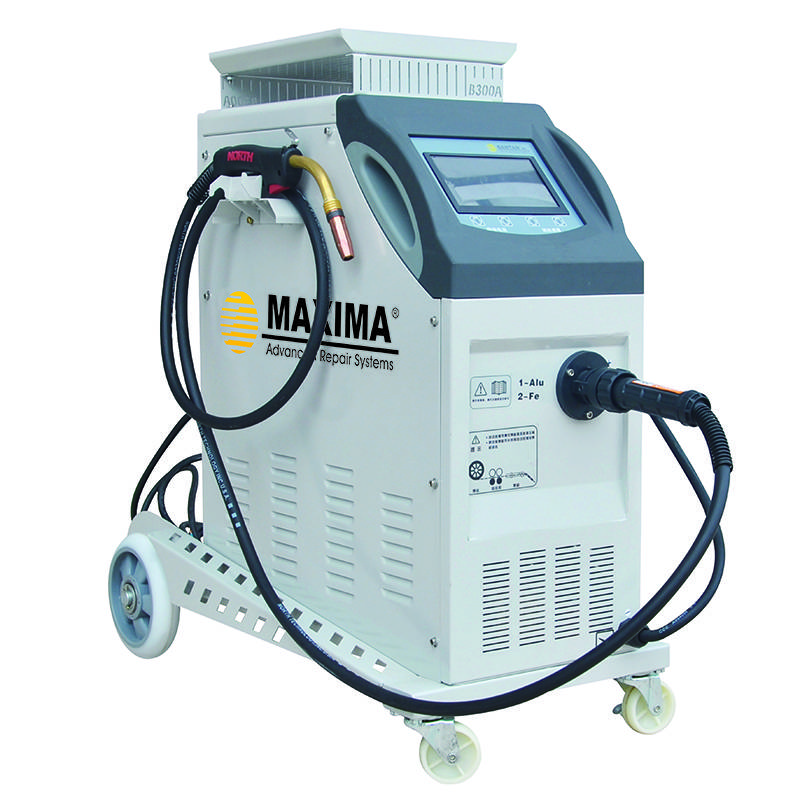
What is gigacasting? Gigacasting uses casting machines to force molten metal into molds under high pressure to produce large aluminum body parts, such as the entire underside of a vehicle. In very basic terms, molten metal is injected into a mold (the “die”), then cooled, ejected, and trimmed.
Where did Tesla CEO Elon Musk get the idea for gigacasting? He examined his child’s die-cast toy cars and thought about ways that it could be replicated for full-sized autos.
What is the traditional approach to automotive manufacturing? Historically, castings have been the predominant product form of automotive manufacturing and have mainly been used in the powertrain of internal combustion engine (ICE) vehicles. The main body of a car has been made by welding or stamping together a large number of separate parts.
Why has gigacasting emerged? Gigacasting using aluminum is one response to the way that massively heavy auto batteries are reshaping how cars are designed. Tesla introduced enormous, high-pressure aluminum die-casting machines that punch out vehicle chassis and bodies-in-white.
Why has gigacasting become so important? Gigacasting has the potential to reduce per-unit manufacturing costs because it eliminates welding dozens of body parts. Instead, it casts one single module. It saves time, labor, cost, and factory space, as it replaces multiple robots that weld car parts together with a single machine.
What took place behind the scenes to make gigacasting a reality for Tesla? Tesla reportedly turned to firms that make test molds out of industrial sand with 3D printers. Using a digital design file, printers known as binder jets deposit a liquid binding agent onto a thin layer of sand and gradually build a mold, layer by layer, that can die cast molten alloys. The cost of the design validation process with sand casting costs about 3% of doing the same thing with a metal prototype. Tesla was able to tweak prototypes as many times as needed, reprinting a new one in a matter of hours using machines from companies such as Desktop Metal and its ExOne unit. The design validation cycle using sand casting only takes to 2 to 3 months, compared with anywhere from 6 months to a year for a mold made from metal.
How does the Model Y fit into the gigacasting story? Tesla took gigacasting from theory to practice in 2019 when it used gigacasting to fabricate the rear floor section of the Model Y. It took between 6,000 and 9,000 metric tons of force. Tesla utilizes 2 giant gigacastings that serve as the front and rear underbody in the Model Y, thus revolutionizing traditional car body (unibody) design and streamlining manufacturing. The new approach to production is quickly moving to become an industry standard.
Tell us more about gigacasting and the Model Y production process. The two castings replaced 171 parts, which were mostly sheet stampings along with some smaller castings, eliminated 1,600 welds, and removed 300 robots from the assembly line. All of this reduced required capital investment and floorspace significantly, and now the company can produce a Model Y in 10 hours — about 3 times faster than EVs built by competitors.
How are the gigacastings manufactured? The giant castings are manufactured on a massive machine, known as a gigapress, which is able to achieve 6,000 tons of locking force and is theoretically capable of producing up to 45 castings per hour.
What obstacles did Tesla need to overcome with these large-scale castings? The aluminum alloys used to produce the castings behave differently in molds made of sand than they do in molds made of metal. Early prototypes often failed to meet Tesla’s specifications. The casting specialists overcame those behavioral difference by formulating special alloys, fine tuning the molten alloy cooling process, and coming up with a post-production heat treatment.
Why is gigacasting in the news lately? Musk told employees at the Gruenheide gigafactory last week that it would soon be manufacturing a new, smaller EV that will retail for around $25,000. This gigafactory is home to Tesla’s gigapress technology, which the company has said will enable it to manufacture EVs more cheaply with fewer parts. The 400 parts that are needed in a conventional car do a number on profitability. A single large frame — combining the front and rear sections with the middle underbody where the battery is housed — could be used toward manufacturing this affordable Tesla EV.
Why aren’t all manufacturers embracing gigacasting? Vehicles with a single molded underbody would no longer allow changing one damaged part in a vehicle and might increase the number of vehicles that are determined to be too costly to repair. S&P Global notes that there are enormous initial startup costs to gigacasting, and the process may yield distortion issues in the metal. Collision repairs change drastically. Inspection scanning at the end of line is extensive.
Are automakers other than Tesla incorporating gigacasting? Volvo hopes to develop several vehicle models that can make use of what it calls “megacasting” for its body-in-white elements. The castings will integrate even mounting points for components such as suspension arms and electric motors. General Motors chief executive Mary Barra said in 2022 that the company had ordered two “gigapress” machines with the intention of using the technology for mass-market vehicles.
Will Toyota adopt Tesla’s model? Not exactly. Instead, Toyota’s Production System, which is based on just-in-time manufacturing efficiency, will rely on its decades of experience to find its own innovations necessary to produce millions of vehicles each year in multiple configurations. Toyota told the Financial Times it wants more than half of its 2030 sales target to be made up of EVs using its new modular architecture, which allows it to produce different models that share key components on the same platforms. The company does need reconfiguration, though, to remain competitive.
Carolyn Fortuna, PhD, is a writer, researcher, and educator with a lifelong dedication to ecojustice. Carolyn has won awards from the Anti-Defamation League, The International Literacy Association, and The Leavey Foundation. Carolyn is a small-time investor in Tesla and an owner of a 2022 Tesla Model Y as well as a 2017 Chevy Bolt. Please follow Carolyn on Twitter and Facebook.
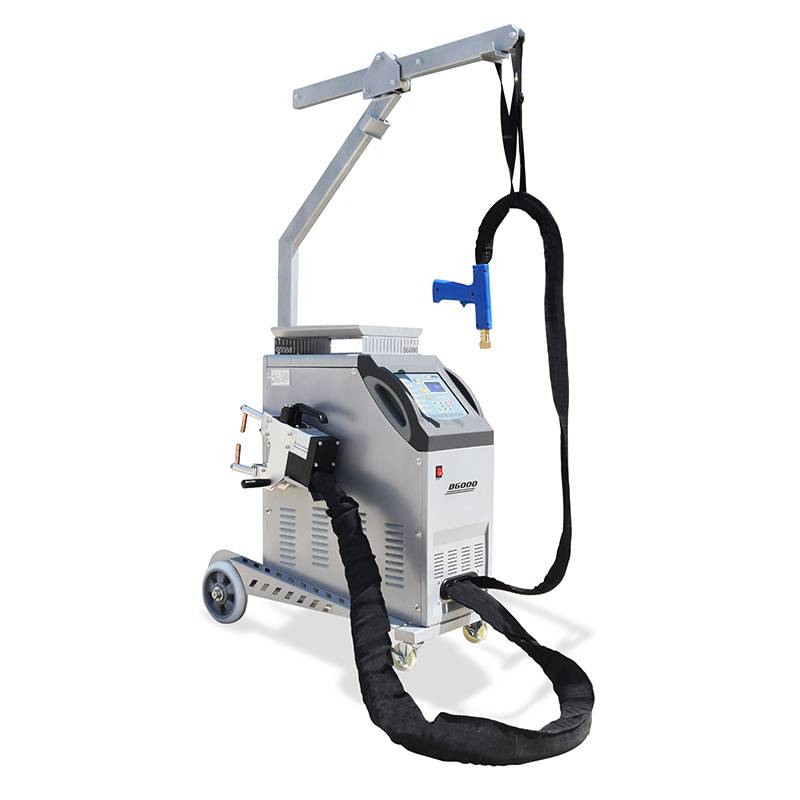
Bus Mobile Lift Carolyn Fortuna has 1231 posts and counting. See all posts by Carolyn Fortuna