As laser manufacturing systems for sheet and tube grow more sophisticated—powerful, automated and scalable—navigating the wealth of choices might feel daunting. But with a little imagination and collaboration, fabricators of all sizes can craft a robust system that meets current and projected production needs.
While different fabricators use lasers differently, the ultimate goals are generally the same: eliminate secondary operations with systems customized to one’s business. Square Tube Round Tube Metal Pipe Processing

A review of offerings from top system providers illustrates, among other options, a growing number of combination machines and customized system options. From employing multiple lasers to updatable cutting process libraries and moving and storing high volumes of material, systems are more flexible than ever.
While CO2 systems are still available for particularly thick materials, fiber lasers continue to gain ground thanks to being easier to operate and maintain. Controllers are more functional, and machine connectivity as well as data collection and sharing are more fluid. Not only that, but controllers appear “cleaner,” featuring touch screens instead of buttons and switches. The user-friendliness of today’s laser manufacturing systems helps solve for the continued scarcity of highly skilled production workers.
Expanding on its solutions for all-in-one-system processing, Amada America Inc., Buena Park, Calif., has expanded on its ENSIS platform to offer the ENSIS RI Rotary combination system. Currently at 3 kW, the fiber version of the ENSIS RI appeared two years ago as a substitute for the longstanding CO2 version.
The ENSIS RI platform, a flat-sheet laser with rotary attachment, features full dual-pallet 5 × 10' (1.52 × 3.04 m) cutting for up to 1" (25.4 mm) plate, explained Laser Division Product Manager Dustin Diehl. With shuttle tables in and out the front of the system, “we take those shuttle tables, put them back into the pallet changer, then introduce a third cutting pallet from the rear of the machine. Within two minutes you can go from cutting 1" [25.4 mm] mild steel or 22-gauge stainless—and with a shuttle exchange, you can bring a third pallet in from the rear and you have a full rotary index machine able to process a 20' [6.08-m] piece.”
That level of flexibility means job shops can “quote jobs they weren’t previously able to do,” he explained, “maybe some complex handrail or tube geometry that didn’t fit within the shop or was going to be labor intensive. ENSIS RI lets [a shop] quote the entire package and run it through one machine by eliminating a lot of secondary processes, instead of having a sawing operation, then taking the material to a drilling operation or a Bridgeport mill for internal geometry.”
OEMs can also benefit from the RI’s versatility, he added. “I think the days of really large inventories and WIP (work-in-progress) are over. People are switching to more kit manufacturing. This machine makes it simple to cut flat sheet and then—on the same job with a couple of minutes of transfer time to your tube or angle—process that job as a kit and send it down the line.”
Featuring the same cutting tables as the AJ platform, all cut conditions for the RI are built into the controller and called up automatically for the material designated by CAD/CAM software, whether material sheet or angle, square or rectangle tubing, or round bar, or more. “The machine makes the adjustments automatically to cut accordingly,” said Diehl. “With square tubing, for instance, in the corner of the web of that material it’s going to be a little bit thicker than if it were quarter-wall tubing. The machine knows that and can adjust the speed around the corner and compensate for it being a little bit thicker material.”
One key to this automatic material detection is the Z height sensor, which “senses material just as it would in flat sheet. It also knows the radius of square tubing or angle; it can go through the process of interpolation and know where it’s going to be processing from one surface around the corner to the next,” he said. “It doesn’t have to rely on the sensing—it actually knows where it’s going, so it makes for fast tube processing.”
In fact, Amada initially envisioned the RI platform would generally be used for roughly 70 to 80 percent flat sheet and 20 to 30 percent tube. “We had so many customers come back to us after finding so many applications on the tube side that they are running it 50-50. They’ll run all their round stock and tubing on the first shift, then on second shift they will process all their flat steel.”
And while the ENSIS RI is working on one job, an operator can be setting up another—for instance, by inserting the requisite jaws into the chuck for a tube job. And with 3 kW of power, it cuts 1" (25.4-mm) mild steel, ½" (12.7-mm) stainless and aluminum, ¼" (6.35-mm) copper and 5/16" (7.94-mm) brass, using oxygen, nitrogen or shop air as appropriate. “Nitrogen cutting is popular,” Diehl noted, with its clean cuts particularly well suited for combination work. For a powder coating application, for instance, “you don’t have to do any oxide descaling; the part is ready to go right on the powder coat line.”
To keep the laser running smoothly, built-in monitoring can detect suboptimal conditions—for instance, a blue plume of plasma above the material that could result in the machine not cutting but virtually welding. The RI “will slow the feed rate while continuing to get through the material, and at the next piece of geometry will bring it back up to full speed or the desired condition.” Upgrades from the CO2 version include a touch probe on the rotary index side of the machine to detect deflection in long pieces of tubing, and work supports motorized to stay in sync with the drive chuck.
A powerful example of a highly automated laser manufacturing system is on display at the new 165,000 ft2 (15,329 m2) headquarters for Bystronic Inc. in Hoffman Estates, Illinois.
In the 30,000 ft2 (2,787 m3) demo space resides a “factory of the future” featuring two lasers: a 12 kW ByStar Fiber with a ByTrans Cross load-unload and a BySort automated parts sorting system, and a 6 kW BySmart fiber with a configurable load-unload with a conveyor outfeed. Both are connected to a 120-location, five-tower material library that can feed both lasers, and both lasers can store parts back into it. Also connected is an automated bending cell with an Xpert 150 robot.
Properly scaling those systems is the expertise of laser cutting pioneer Nicole Amico. In her role as solution center expert, she “typically starts with current pain points and customers’ direct needs. Then I ask them to dream based on their projected growth over the past five years and what the next five years might look like. The best way to scale something is to have a tangible picture of what the final system looks like, then back up five years. A lot of times we create a big picture then bite that off in [individual] capital investments. It gives them—and us—a way to look at their facility and infrastructure and see how well this will fit.”
While obsolete equipment might be candidates for unloading to accommodate new, Amico looks to build some existing equipment into Bystronic’s automation solutions. “I can do a single step of load-unload and six months later add parts sorting, six months later add a tower, and six months later add two or three towers I can feed a second laser from. Because it’s so modular, I can do it wide or long and skinny and add it in whatever pieces they want.”
Bystronic also acquired TTM (now Bystronic Tube Processing SpA) in 2018 and followed that with a big commitment to product development. The first result of this effort is the ByTube130, which is aiming to be the fastest 5" (127-mm) tube laser on the market. This will complete the lineup of tube lasers that runs up to 24" (610-mm) diameter in order to handle extremely heavy structural steel.
Continuous improvement of automation options at Bystronic is fostered by consultation sessions combined with customer feedback. For instance, when scaling up bed sizes from 3015 (3 × 1.5 m) to 8025 (8 × 2.5 m), automation was scaled concurrently. One improvement to handle increased payload when processing large-format plates was on the unloading forks. Bystronic upgraded the linear guides and heavier moving components so customers could process the complete thickness and size range of material in a fully automated manner on any size laser. The same attention to detail goes into the company’s Industry 4.0 software.
Ultimately, customers’ needs run the gamut—and suppliers must meet the challenge, Amico asserted. “Some customers have all their press brakes and lasers integrated; some are only looking for more uptime from their lasers.” And it’s not just physical equipment concerns, but the physics of laser production that should be addressed, she added.
Murata Machinery USA Inc., Charlotte, N.C. offers two types of hybrid fiber laser systems that incorporate two or three processes into a single machine, said Jeff Tyl, North American sales manager of fabrication.
“A lot of small sheet metal fabricators are using lasers to blank parts or for parts that don’t have any forming and then they are [using] a secondary process after the fact—whether it be tapping, drilling or forming,” he explained. Muratec combination machines—the advanced hybrid laser LS series and the hybrid punch laser MF series—“give the fabricator an opportunity to minimize floor space, process and turnover.”
With rack-and-pinion, laser-based punch hybrids, Tyl noted, the table and head move “so to cut you have to be able to workhold, and you can only laser-cut as thick as you can hold; a lot of times, that is 3/8" [9.53 mm] and below.” For fabricators that want to cut thicker materials, Muratec’s hybrid “is a laser machine first and foremost” with forming and tapping capabilities that let users cut everything from very thin material up to about 1¼" (31.75 mm), then form and tap up to ½" (12.7 mm).
“We have a customer who has both laser and punch machines,” Tyl said. “They’re blanking off their laser, so they’re cutting some profiles with holes, then taking the part to a turret punch to do louvers, embosses and scribe lines. They’re using two separate machines for a single process. We’ve talked to them about going with our laser-based hybrid,” which the customer can use as a laser on its own or also perform embossing, etching, drilling and tapping. “It’s a rigid tap, so you can do a pre-pierced hole, and then it doesn’t work-harden the threads.”
For lights-out production, users can also add a pallet loader to the pallet changer that comes standard with the machine. The available tower can store multiple drawers of different grades, thicknesses and sizes of material. A parts-sorting system can complete the full automation package.
Murata offers options in beam delivery cables in three different thicknesses measured in microns (μm). “Edge quality changes as the size of beam and fiber change in [microns],” Tyl explained. “In our 2.5 kW and 4 kW, we are offering 50 μm (the average human hair is 70 to 120 μm). When it comes to cut quality (for 3/8" [9.53 mm] and below), you are getting very small ridges. Up to 6 kW, we offer an 80 μm option that cuts a little bit thicker and a little faster. The ridges start to get a little larger because of the slightly larger wire. Above 6 kW, we offer 100 μm; to produce ¾" [19.05 mm] and above, the thicker the [beam delivery cable] the better.”
To handle multiple thicknesses, Murata continually develops cut conditions. “If you are using a nozzle for ¼" [6.35 mm] mild steel, if you went to 3/8" [9.53 mm] mild steel or 3/16" [4.76 mm] mild steel, a lot of times those cut conditions don’t change a lot other than the focus point; you would use the same nozzle,” Tyl explained. “But for stainless, you may change the nozzle size and focus size; that is a predetermined number in our system. When you put the program into our system, it tells what it should start with, and you do some tweaking from there”—for example, moving the focal point up or down depending on the appearance of dross, burrs and ridges.
Murata’s hybrid laser machines are finding interest in high-tolerance medical applications as well as among mom-and-pop machine shops “that really want to be competitive. Our last four laser installations went to mom-and-pop shops,” Tyl said.
For 2D sheet and tube cutting, Platino and Laser Genius platforms fill the bill. Both are available from Prima Power North America Inc., Arlington Heights, Illinois. About 90 percent of customers are moving to fiber in the Platino platform, noted 2D Laser Product Manager Simone Bonetto, but CO2 still is the choice for fabricators that either deal with a high volume of thick materials or that do not have the budget for the fiber machine.
The available Compact Server package provides a cassette for loading and another for unloading. “Customers can get additional interchangeable shelves so production never stops,” Bonetto said.
For shops that are new to lasers, the ball-screw Platino in 4 kW or 6 kW is an ideal choice, he explained, while the linear drive Laser Genius is available up to 10 kW. “If you are cutting mostly parts without many profiles inside, and you cut a variety of materials and thickness combinations, then Platino is perfect. If you’re going to do a lot of hole-intensive parts, the Laser Genius can perform better at higher production volumes.”
To maintain optimum piercing, Prima Power’s systems feature sensors to monitor light intensity and avoid anomalies. A nitrogen-assisted system is optional to accelerate processing.
A unique feature of Prima Power’s systems, Bonetto noted, is the cantilever design. “The Y-axis carriage is attached on only one side of the machine, which gives customers the opportunity to access the machine on three sides: top, side and front. Sometimes you need to interrupt a high-volume process and run a couple of parts quickly. If you have a completely enclosed design, you cannot do that. Our system allows you to stop production, open the cabin, throw in a piece of metal and cut a couple of parts, then remove those parts and resume the previous job,” he said.
To expand the usability of its TruLaser Tube 5000 and 7000 machines, Trumpf Inc., Farmington, Conn., added a pair of significant upgrades:
“About a third of the machines we sell have the spindle,” noted Account Manager Thomas Burdel. The spindle can also use Flowdrills to create extra threads in thin material, eliminating the need for inserts.
The loading towers, developed over the past couple of years, can load round, square or rectangle tube directly. “Flat sheet cutting is much more advanced on the loading side,” Burdel explained. “Integrated towers, where you can switch one tube type to another automatically, will change the industry.”
The TruLaser Tube 5000 handles tube up to 6" (152.4 mm) in diameter, the 7000 up to 10" (254 mm) in diameter. Tube length can vary from 21 to 30' (6.4 to 9.14 m) on the loading side.
The former machine is available up to 3 kW, the latter up to 4 kW. The machines can also cut flat stock, like busbars, up to 3/8" (9.53-mm) thick and 9" (228.6-mm) wide.
Depending on applications, which range from agricultural equipment to furniture, each machine’s footprint is customizable from 10 to 26' (3.05 to 7.92 m) on the unload side. He noted that the most common tube length in the U.S. is 24' (7.32 m).
With 40 years in the laser manufacturing industry, including a fair amount of that building CO2 lasers, Mark Barry of Prima Power Laserdyne, Minneapolis, offered some sage advice for fabricators new or familiar with laser manufacturing.
“There are a lot of game changing things going on,” said Barry, vice president of sales and marketing for Laserdyne. “An interesting aspect about laser processing is that we can add on after the fact.”
When seeking a supplier, he advised, the amount of attention given from setup to continued training is a key distinguishing factor.
“For somebody cutting sheet metal, any good supplier is going to give them a series of tables to get them going. What we like to tell people is that this is the starting point—don’t take it as gospel. What a good cut on 316 stainless steel is to me might be entirely different to you, and more importantly to your customer base. These tables should have the flexibility of being adapted. Say initially you have 30 tables. If I come back in six months and you still have 30 tables, something’s not right; you should have 45 or so.”
After the initial system planning, purchase and setup, continued training is another perk that the best suppliers provide, Barry continued. “It’s not uncommon after several years of use that a new set of engineers is taking over. How long does training take? It depends on where those engineers are coming from. Do they understand CNC? Do they have any idea of what laser processing is? What do they want to do? The job shop wants to do a lot of different things, whereas a large OEM may buy a machine and have the volume to have one part go through it.”
For shops new to laser systems, having people well-versed in production of 3D parts eases the transition into laser production, Barry noted. “Understanding laser processing is not that difficult. When somebody asks me who they should consider as a technician or operator, I want somebody who understands multiple-axis machining.”
Putting the right system in place often begins with plant tour, said Bystronic’s Brendon DiVincenzo, product manager for laser and automation. Material flow through one’s production space is critical to analyze, as the speed and efficiency of fiber lasers can significantly stress current capacity.
“These fiber lasers are so fast that if you’re replacing a traditional 4 kW, CO2 machine with a 6 kW or 10 kW fiber laser, suddenly you have the capability of going through four to five times more sheet or parts per shift,” said DiVincenzo. Physical bottlenecks are also a problem. It might be easy to deal with a situation where carts have to get out of each other’s way in an aisle four to five times a shift—but not so easy if that is happening 25 or 30 times a shift.
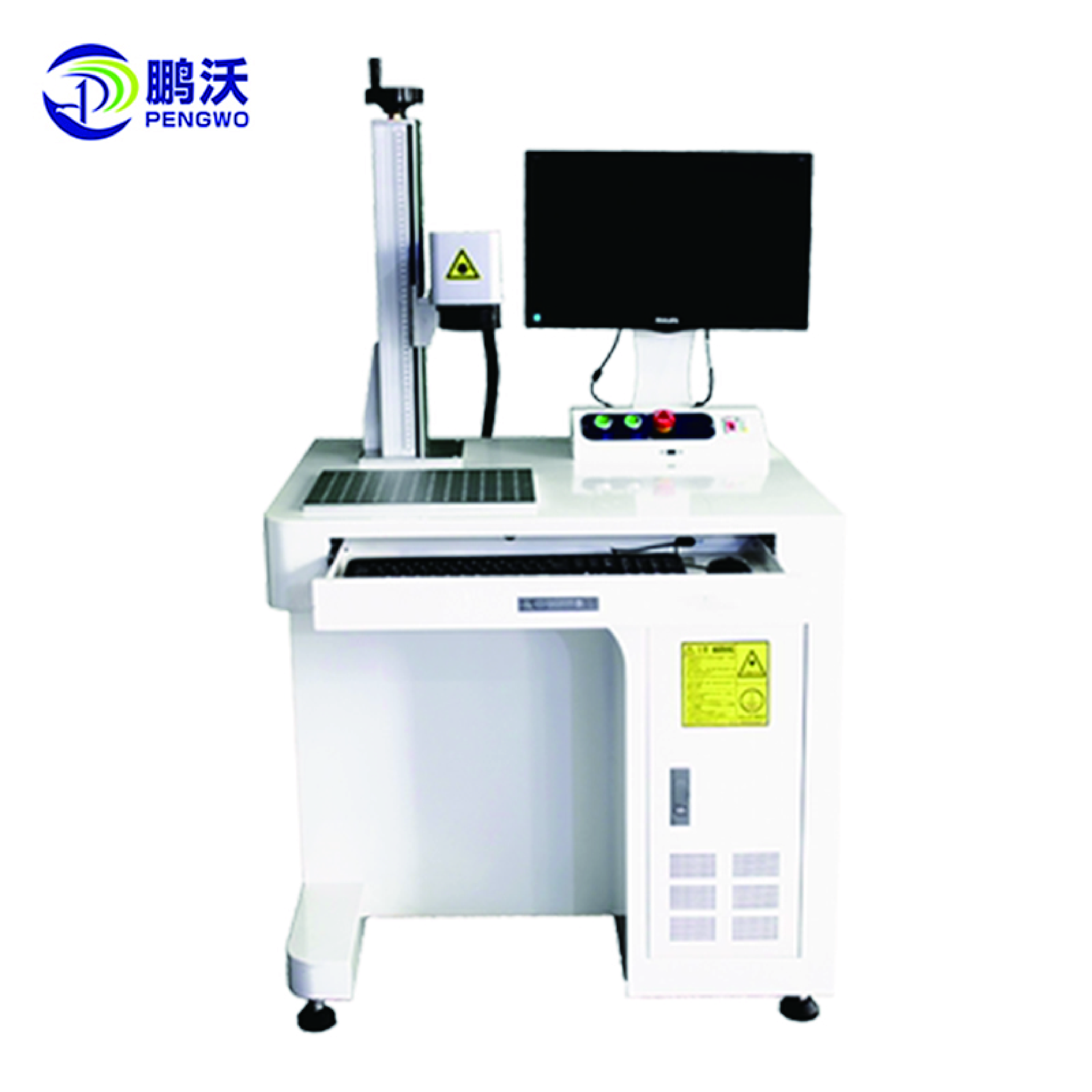
Desktop CNC Metal Plasma Cutting Machine Ultimately, “The one thing that stays the same is every system tends to be a little bit different,” he concluded. |||